Feed Mill Production Technologies and Equipment: A Modern Perspective
Gain comprehensive knowledge about the fundamental production technologies and equipment (grinding, mixing, pelleting, cooling, sieving, etc.) used in feed mills, from raw material reception to packaging.
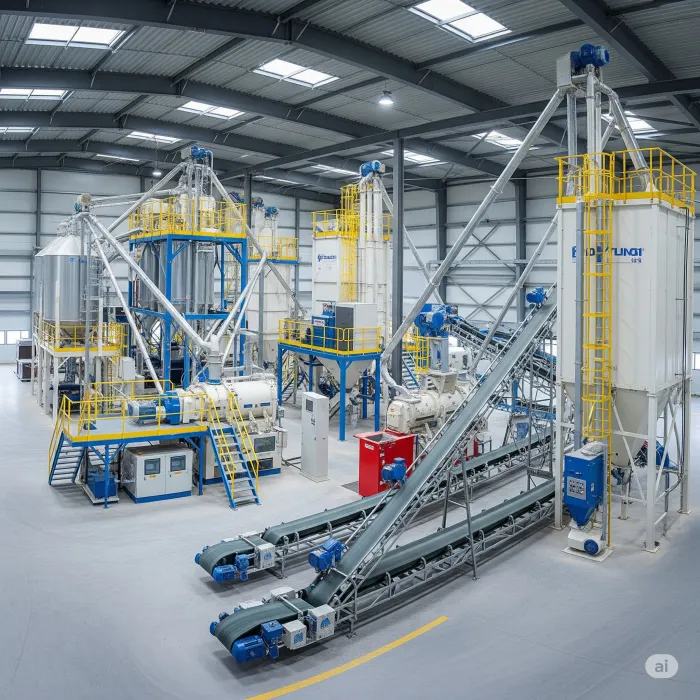
Feed Mill Production Technologies and Equipment: A Modern Perspective
---Feed production, a cornerstone of modern animal husbandry, requires advanced technologies and specialized equipment to provide the nutrients animals need in the most efficient and hygienic way. A feed mill goes through a series of complex stages, from the arrival of raw materials to the packaging of the final product. Each piece of equipment and technology used in this process directly affects the quality, digestibility, and cost of the final product.
So, what are the main production technologies and equipment used in a feed mill? Here are the primary stages and the critical machines involved:
1. Raw Material Receiving and Storage
The first step in the production process is receiving raw materials (grains, meals, additives, etc.) that arrive at the factory and storing them securely.
- Equipment:
- Weighbridge: For accurately measuring the weight of incoming raw materials.
- Receiving Pits and Elevators: For fast and efficient unloading and transfer of raw materials to storage silos.
- Storage Silos/Warehouses: To store raw materials, protecting them from moisture, pests, and spoilage. Separate storage areas suitable for each raw material are critically important.
2. Pre-Cleaning and Separation
Before stored raw materials are introduced into the production line, removing foreign materials (stones, metal, strings, debris, etc.) is vital for both protecting the equipment and ensuring the quality of the final feed.
- Equipment:
- Pre-Cleaners/Screens: Used to separate large and small foreign materials.
- Magnets: Attract and separate metal particles, preventing metal contamination in the feed and damage to subsequent machines (especially grinders).
- Air Separators: For separating dust and light particles.
3. Grinding (Milling)
Reducing raw materials to smaller and more uniform particle sizes is necessary to increase digestibility and facilitate the mixing process. The degree of grinding is adjusted according to the animal species and the purpose of the ration.
- Equipment:
- Hammer Mills: The most commonly used grinding equipment. High-speed rotating hammers reduce raw materials to the desired fineness through screens. Different screen sizes allow for different grinding fineness.
- Roller Mills: Used especially for coarser grinding or rolling of grains like corn. They produce less dust and allow for more controlled particle size adjustment.
4. Mixing
Homogeneous distribution of ground raw materials, vitamins, minerals, and other additives ensures that animals receive balanced nutrition with every bite. This is one of the most critical stages of feed production.
- Equipment:
- Horizontal Mixers: The most common mixer type. They mix raw materials quickly and homogeneously using paddles or ribbons inside. Generally ideal for dry mixing.
- Vertical Mixers: Operate slower and consume less energy. Generally suitable for mixing larger particles.
- Liquid Spraying Units: Ensure uniform addition of liquid additives like molasses and oil to the ration during mixing.
5. Pelleting (Granulation)
Pelleting, particularly preferred for poultry and fish feeds, involves compressing the powdered feed mixture under heat, moisture, and pressure to form small, cylindrical pellets.
- Equipment:
- Conditioners: The section where the feed mixture is heated and moistened with steam before pelleting. This promotes starch gelatinization and improves pellet quality.
- Pellet Mills: The main machine that forms pellets by forcing the feed mixture through dies at high pressure. Compression is achieved through friction between the die and rollers.
- Pellet Cutters: Cut long pellets to the desired sizes.
6. Cooling
Pellets that reach high temperatures during the pelleting process need to be rapidly cooled to prevent spoilage during storage and transport. Cooling also increases the hardness and durability of the pellets.
- Equipment:
- Counterflow Coolers: One of the most efficient cooling systems. As pellets move downwards, cold air flows upwards, maximizing heat transfer.
- Horizontal Coolers: Occupy less space and provide continuous flow.
7. Sieving and Crushing (Crumbling)
Sieving out fine dust and broken pieces from cooled pellets is important for obtaining a homogeneous product. For some animal species (especially chicks), pellets are crushed into smaller "crumble" feeds.
- Equipment:
- Sifters: Separate pellets according to desired size, removing fine dust and broken pieces. Dust separated by the sieve is usually sent back to the pelleting line.
- Crumbler: Equipment that crushes pellets into smaller, irregular crumbles.
8. Packaging and Storage
Finished feeds are packaged for storage and distribution.
- Equipment:
- Bagging Machines: Fill feeds into bags of specific weights and seal them.
- Big Bag Filling Systems: For filling larger volumes of feed (500 kg - 1000 kg) into large sacks.
- Storage Areas: Warehouses where packaged products are stored until shipment, protected from moisture and pests.
Conclusion
Production technologies and equipment in feed mills combine the science and engineering of animal nutrition to transform raw materials into high-quality and safe feed products. Proper equipment selection and operational efficiency at each stage directly affect both feed quality and mill profitability. Modern facilities optimize these processes further through automation systems and advanced control mechanisms, ensuring sustainable and efficient production.
Which production stage in feed mills interests you the most? Share your thoughts with us in the comments!