Energy Costs and Management in Feed Mills
Learn about energy consumption areas, factors affecting costs, and strategies to reduce energy costs in feed mills. Discover the importance of energy efficiency for sustainable production.
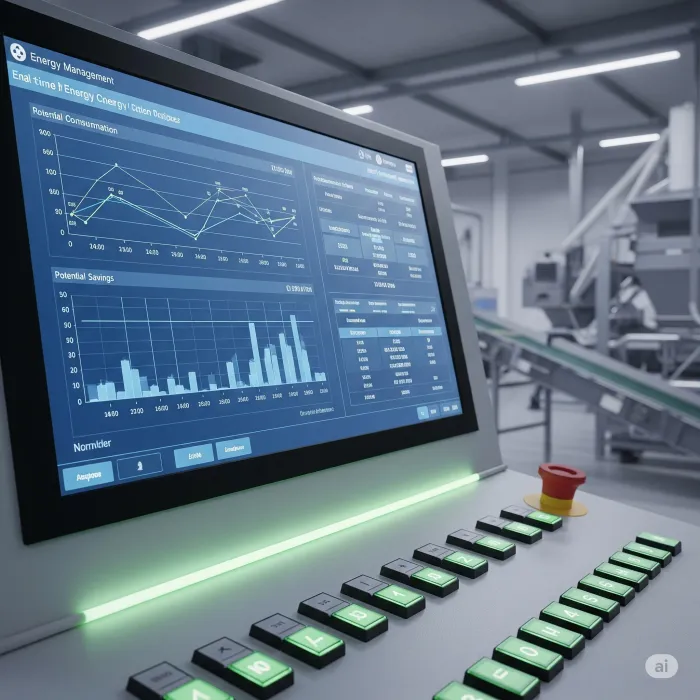
Energy Costs and Management in Feed Mills
Feed mills are facilities that consume significant amounts of energy due to their complex production processes and large-scale operations. Energy sources such as electricity, natural gas, and fuel play a critical role in determining feed costs and overall profitability. As **energy costs** constantly fluctuate, effective management of these costs is key to ensuring sustainability and competitive advantage for feed mills. So, what are the main energy cost items in feed mills, and how can these costs be managed?
Primary Areas of Energy Consumption
In a feed mill, energy consumption occurs at almost every stage of the production process:
1. **Grinding (Milling):** Mills (hammer mills, etc.) used for grinding raw materials consume high amounts of energy. Fine grinding of coarse-grained raw materials, in particular, requires more energy.
2. **Pelleting:** The process of forming feed into pellets is a high-pressure operation performed by pellet presses. These machines consume a significant amount of electricity due to their motor power and friction. Additionally, energy (usually natural gas) is used for steam generation.
3. **Drying and Cooling:** Drying the moist feed after pelleting and then cooling it are also energy-intensive processes. Dryers typically use natural gas or other fuels, while coolers consume electricity through fans.
4. **Mixing and Dosing:** Mixers and dosing systems used for precisely mixing raw materials operate on electrical energy.
5. **Conveying and Storage Systems:** Material handling systems such as conveyors, elevators, pneumatic conveying systems, and silo loading/unloading equipment continuously consume electricity.
6. **Steam Generation:** Steam is used to condition the feed before pelleting. Steam boilers typically run on fuels like natural gas or fuel oil and constitute a significant portion of the factory's energy bill.
7. **Lighting and Heating/Cooling:** The lighting of factory buildings and the heating/cooling needs of administrative offices and production areas also contribute to overall energy consumption.
Factors Affecting Energy Costs
Fluctuations in energy costs depend on many factors:
- **Global Energy Prices:** World market prices for primary energy sources such as oil, natural gas, and coal.
- **Exchange Rates:** In countries dependent on energy imports, increases in exchange rates directly raise energy costs.
- **Energy Policies and Taxes:** Government energy policies, subsidies, or taxes affect energy prices.
- **Energy Efficiency Standards:** New regulations or industry standards may necessitate investment in energy-efficient equipment.
- **Technological Advancements:** Developments in energy-efficient equipment and process technologies offer the potential for long-term cost reduction.
Methods for Managing and Reducing Energy Costs
Feed mills can implement various strategies to reduce and manage energy costs:
1. **Energy Audit and Monitoring:**
- **Comprehensive Energy Audit:** Detailed energy audits should be conducted to identify all energy consumption points in the factory, pinpoint areas of waste, and reveal potential savings.
- **Implementation of an Energy Management System:** By installing systems that monitor and analyze energy consumption in real-time (e.g., Energy Management Software), anomalies can be quickly detected and corrective measures taken.
2. **Equipment Modernization and Efficiency:**
- **Investment in High-Efficiency Equipment:** Replacing old and inefficient machines with new-generation, energy-efficient equipment that consumes less energy, especially in energy-intensive processes like grinding, pelleting, and steam generation. For example, using IE3 or IE4 efficiency class motors.
- **Variable Frequency Drives (VFDs):** Optimizing energy consumption by using VFDs that adjust motor speed according to need, resulting in significant savings, especially in continuously operating equipment like fans and pumps.
- **Heat Recovery Systems:** Utilizing waste heat from post-pelleting cooling or drying ovens in other processes, such as steam generation or preheating feed.
3. **Process Optimization:**
- **Pelleting Optimization:** Ensuring the most efficient settings for pellet presses (die selection, compression ratio, etc.) and conditioning the feed at optimum moisture reduces the energy required for pelleting.
- **Adjusting Grinding Fineness:** In cases where the finest grinding is not always necessary, energy consumption of mills can be reduced by selecting the appropriate grinding fineness.
- **Efficient Steam Management:** Preventing leaks in steam lines, recovering condensate, and efficiently operating steam boilers reduce fuel consumption.
4. **Renewable Energy Sources:**
- **Solar Energy (Photovoltaic Panels):** Meeting a portion of electricity needs by installing solar panels on factory roofs or suitable areas.
- **Biomass:** Evaluating the potential for energy generation from factory waste or local biomass sources.
5. **Maintenance and Good Operating Practices:**
- **Regular Maintenance:** Regular maintenance of all equipment (lubrication, cleaning, adjustment) reduces friction and increases efficiency, thereby decreasing energy consumption.
- **Leak Prevention:** Detecting and eliminating leaks in air, steam, or water lines prevents energy waste.
- **Personnel Training:** Raising awareness among employees about energy saving and encouraging good operating practices (turning off unnecessary lights, not running motors idly, etc.).
Conclusion
Managing energy costs in feed mills is a strategic issue that requires continuous monitoring, technological investments, and operational discipline. While investments in energy efficiency may seem costly initially, they provide significant returns in the long term, increasing the profitability of businesses and contributing to environmental sustainability. The competitive feed mills of the future will be those that intelligently manage energy costs and adopt green energy solutions.