Optimizing Production Processes and Cost Reduction Methods in Feed Mills
Discover methods to optimize production processes and reduce costs in feed mills. Learn all the steps from raw material management to energy efficiency, automation, and maintenance.
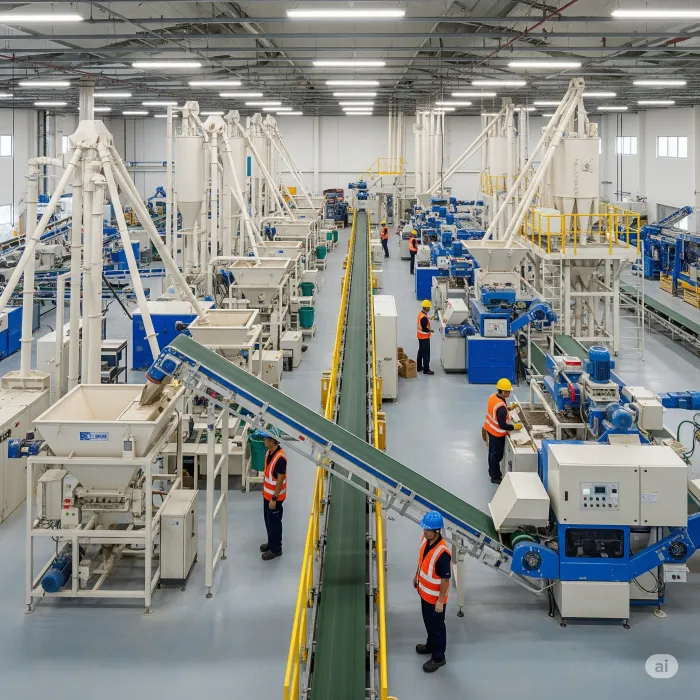
Optimizing Production Processes and Cost Reduction Methods in Feed Mills
Feed production is one of the cornerstones of the livestock sector and has a direct impact on profitability. **Optimizing production processes** and **reducing costs** in feed mills not only provides a competitive advantage but also improves the quality of the final product. So, what can a feed mill do to operate more efficiently and produce at lower costs?
Why Is Optimization Important?
Feed mills are facilities that process large amounts of raw materials, consume energy, and require labor. In this complex structure, every small improvement can lead to significant savings. Optimization ensures the most efficient use of resources, reducing waste and increasing profitability.
Methods for Optimizing Production Processes
Here are steps that can be taken to increase efficiency in production processes:
1. **Smart Raw Material Management:**
- **Supply Chain Optimization:** Establishing strong relationships with suppliers is crucial to procure raw materials at the best price, quality, and on time. Bulk purchases or long-term contracts can provide a price advantage.
- **Inventory Management:** Excess inventory increases storage costs, while insufficient inventory can bring production to a halt. Adjusting inventory levels according to need (approaching JIT - Just-In-Time principles) both reduces costs and preserves freshness.
- **Quality-Controlled Procurement:** Raw material quality directly affects the quality of the final product and production efficiency. Low-quality or contaminated raw materials can cause problems in the production line and increase reprocessing costs. Therefore, rigorous **raw material receiving control** is indispensable.
2. **Energy Efficiency:**
- **Equipment Modernization:** Old and inefficient machines (especially motors, mills, pellet presses) consume high energy. Investing in new-generation, energy-efficient equipment that uses less power yields significant long-term savings.
- **Heat Recovery Systems:** Waste heat generated during processes like pelleting and drying can be used in other processes (e.g., preheating feed) to save energy.
- **Lighting and Insulation:** Using energy-efficient lighting systems (LEDs) and ensuring good insulation in factory buildings reduces heating/cooling costs.
3. **Automation and Digitalization:**
- **Process Control Systems (SCADA/DCS):** Monitoring and managing production processes with computer-controlled systems increases precision, reduces human error, and maximizes efficiency. Dosing, mixing, and pelleting parameters can be set more accurately.
- **Robotics and Automated Transport Systems:** Automation in areas like packaging, palletizing, and internal transport reduces labor costs and increases operational speed.
- **Data Analysis:** Analysis of data collected from production (energy consumption, yield, breakdown rates, etc.) provides critical information for identifying bottlenecks and areas for improvement.
4. **Maintenance and Failure Management:**
- **Preventive Maintenance:** Regular maintenance before failures occur prevents unexpected downtimes and high repair costs. Regular lubrication, part replacement, and adjustments extend equipment life.
- **Predictive Maintenance:** Continuously monitoring equipment performance through sensors and predicting potential failures in advance minimizes unplanned downtimes.
5. **Labor Efficiency and Training:**
- **Training and Development:** Continuous training of employees on equipment use, process knowledge, and quality control reduces error rates and increases efficiency.
- **Cross-Training:** Employees being competent in multiple tasks provides flexibility in workforce planning and prevents production disruptions in case of personnel shortages.
- **Workflow Improvement:** Ergonomically arranging workstations and streamlining workflows reduces unnecessary movements and saves time.
Cost Reduction Methods
While the optimization steps mentioned above directly contribute to cost reduction, the following can also be considered:
- **Waste Management and Recycling:** Minimizing waste generated during production, such as dust, broken pellets, or spills, and reprocessing it where possible.
- **Formulation Optimization:** Using feed formulation software to develop feed formulas that meet the animal's nutritional needs at the lowest cost. This software considers the cost and nutritional values of different raw materials to find the optimal mix.
- **Water Management:** Monitoring water consumption, preventing leaks, and recycling water where possible reduces water costs.
- **Review of Administrative Expenses:** Regularly reviewing and optimizing administrative expenses such as office expenditures, insurance, and transportation.
Conclusion
Optimizing production processes and reducing costs in feed mills is not a one-time effort but a continuous process. With advancing technology, new opportunities arise, and factories that capitalize on these opportunities become more competitive and achieve higher quality and more sustainable production. It is important to remember that every small improvement can make a big difference.